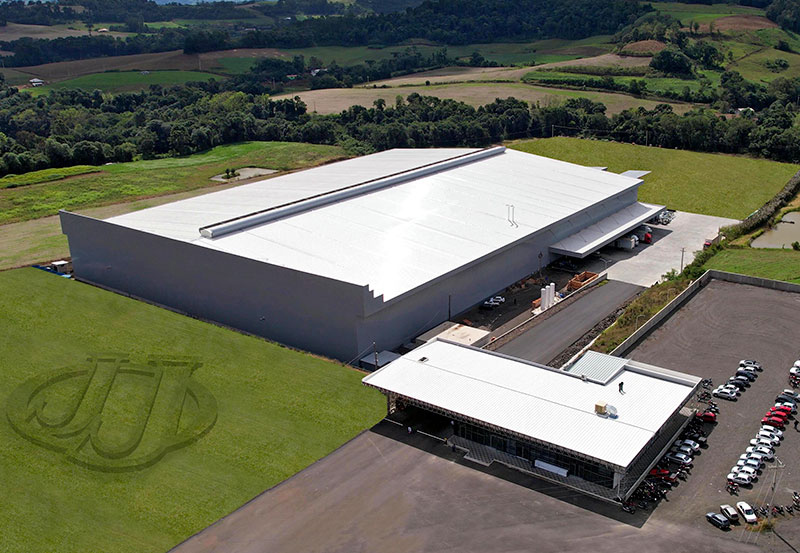
Fábrica da JJ, em Maravilha: redução de movimentações pode chegar a quase 80% - Foto: Divulgação
Localizada em Maravilha, no Extremo Oeste de Santa Catarina, a JJ Instalações Comerciais é especializada na produção de equipamentos expositores como gôndolas, balcões, adegas e sistemas de armazenagem para supermercados. A empresa vem dobrando de tamanho ano após ano desde 2018, e para dar conta da expansão construiu uma fábrica nova. Mas antes de levantar os alicerces a JJ investiu, ainda em 2021, em um projeto de Simulação Computacional junto ao IST Logística de Produção, de Itajaí, para desenvolver o melhor layout possível para seus processos produtivos.
A simulação foi realizada tanto para a unidade nova quanto para a antiga, que ainda não implementou todos os itens sugeridos no projeto. Falta, por exemplo, instalar um rebocador que circulará pelos corredores da planta, coletando e entregando materiais. Mesmo assim o proprietário da empresa, Thiago Simon, afirma que já foi percebida uma economia de 60% em movimentações dentro da indústria – o projeto prevê que a redução chegue a 79%. “Foi o ponto que mais chamou atenção no processo. A movimentação dentro da fábrica antiga estava sendo feita de forma errada, o layout parecia uma teia de aranha. Conseguimos melhorar muito com as opções desenvolvidas através da simulação”, conta Simon.
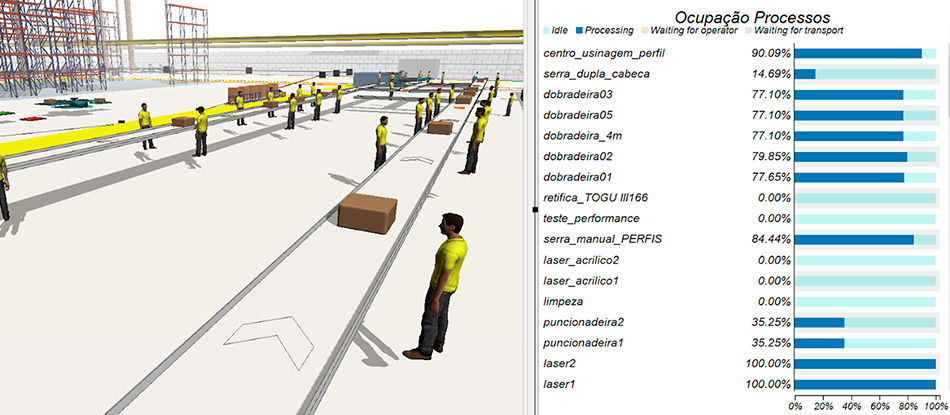
Custo para simulações de processos na JJ foi de R$ 64 mil - Foto: Divulgação
Outra ideia surpreendente que a Simulação Computacional permitiu testar foi a inserção do almoxarifado da nova fábrica no centro da planta, como uma ilha servindo todos os setores. A JJ vem implementando tecnologias da Indústria 4.0, incluindo o uso de robôs, e conta com uma das linhas de pintura mais tecnológicas do País, totalmente autônoma e automatizada. A simulação permitiu inserir a máquina de pintura ao lado da linha de montagem, e não somente no final do processo de corte e dobra, como era na planta anterior. “Havia vários processos da linha de montagem que dependiam da pintura. Nós sabíamos disso, mas não nos dávamos conta do volume de movimentação que isso gerava. A mudança deve trazer ganhos significativos”, informa o empresário.
O IST Logística de Produção começou a oferecer serviços de Simulação Computacional para a indústria e ao setor público em 2013. O primeiro cliente foi a siderúrgica ArcelorMittal, em um projeto em São Francisco do Sul. Desde então, empresas como Britânia, Hering, BRF, Kyly e os portos de Itajaí, Navegantes e Itapoá, além dos departamentos de trânsito de cidades como Itajaí e Xanxerê, já se beneficiam da tecnologia para melhorar processos, identificar gargalos, otimizar o uso de equipamentos, diminuir filas de espera e aumentar a competitividade.
Nilton Bendini Junior, instrutor e consultor sênior do Instituto SENAI e especialista em Simulação Computacional, elaborou o termo “visão de arquibancada” para explicar o potencial de uma simulação para processos complexos como os que ocorrem em uma fábrica. “No futebol existe a visão do técnico, a do jogador e a da arquibancada, de onde se consegue ver o jogo como um todo”, explica Bendini. “A simulação permite enxergar o processo de cima, ver tudo ao mesmo tempo. Isso dá condições de ter insights de forma muito mais rápida, e com comprovação, para tomar decisões e realizar mudanças.”
O processo de Simulação Computacional tem cinco etapas. As duas primeiras são de criação e validação do cenário inicial, que inclui a coleta de dados. Em seguida vêm as fases de desenho de soluções propostas, experimentação de cenários e avaliação dos resultados. O software permite criar situações de forma muito rápida, determinando, por exemplo, quantos metros o colaborador andou, quanto tempo ficou carregando e descarregando, quanto tempo ficou ocioso. O sistema pode prever comportamentos, quebra de máquinas e avaliar o que um novo equipamento traria de benefício para os processos. “É uma simulação da realidade, muito mais dinâmica que uma planilha de Excel”, argumenta Bendini.
Os resultados são apresentados de forma didática, em painéis e em demonstrações que lembram jogos de computador. Há também uso de óculos de realidade virtual para um “passeio” pela fábrica simulada. Finalizado o processo, o Instituto entrega a simulação para o cliente com uma interface que permite fazer outros testes e ajustes de forma independente.
Os investimentos realizados na fase de projeto são dissipados rapidamente durante a execução, quando há não apenas mais retorno financeiro, mas também aceleração nos resultados. “O que estamos fazendo, no caso da JJ, por exemplo, é eliminar tempo de movimentação e converter em tempo de produção”, resume Bendini.
A Electro Aço Altona, de Blumenau, começou a se valer de simulações computacionais em 2017, primeiramente focada em um único setor. Os resultados obtidos fizeram a quase centenária empresa de fundição e usinagem apostar em um projeto de grande envergadura: simular e, talvez, reformular todos os setores da planta de 113 mil metros quadrados para fazer frente a um aumento de demanda que a fábrica não conseguia atender. “A empresa tem muitos setores, nosso processo envolve muitas áreas de atuação, e chegamos a um limite. Não conseguíamos simular internamente todos os subprocessos ao mesmo tempo, mas com as ferramentas da Simulação Computacional isso foi possível”, diz Danilo Correia, diretor industrial da Altona.
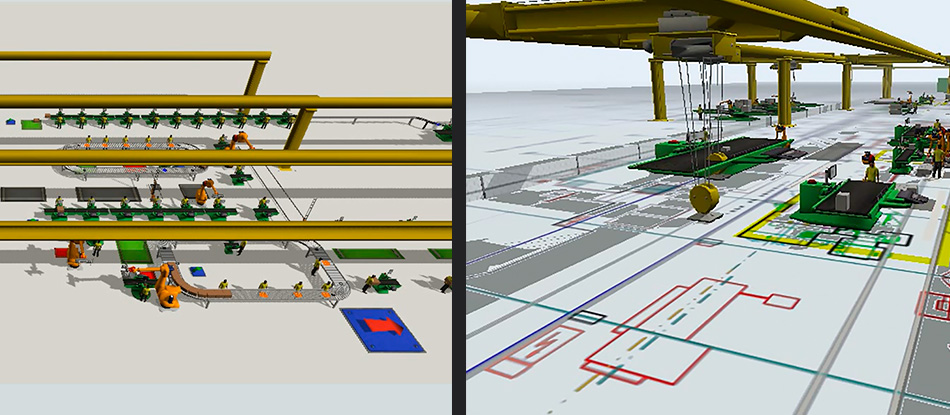
Simulações na Electro Aço Altona: projetos podem levar à reformulação de toda a planta industrial - Foto: Divulgação
A Simulação Computacional completa, realizada pelo Instituto SENAI, permitiu uma visão mais assertiva dos gargalos e se transformou em um verdadeiro plano diretor para a empresa. As principais mudanças já realizadas incluem uma alteração na linha de peças pós-usinagem, mudando a forma de operação de cada trabalhador, e a inserção de um robô para fazer o lixamento das peças, permitindo uma maior padronização da entrega das peças para a fase seguinte de produção e diminuindo o retrabalho. Com as alterações propostas, a empresa aumentou em quase 40% a entrega da fábrica: de 800 toneladas para 1.100 toneladas por mês. O primeiro projeto, de 2017, já havia dividido o setor de moldagem em duas linhas e obtido ganhos de 50% de produtividade.
A empresa constatou que um dos principais benefícios da Simulação Computacional é dar confiança para quebrar paradigmas e tomar decisões que custam caro e precisam dar retorno. “Trabalhamos com duas unidades de negócio que se cruzam durante a produção. São processos diferentes, o que torna tudo muito complexo, difícil de visualizar em um papel ou uma planilha. A simulação traz essa confiança, e facilita até mesmo a mudança de cultura dentro da empresa”, analisa o especialista em gestão de recursos e capacidade, Guilherme Mendes. Ele acredita que a parceria com o Instituto SENAI será um projeto contínuo. “Estamos sempre alterando produtos e processos. Não vejo mais a Altona fazendo grandes mudanças sem simular antes”, conclui Mendes.