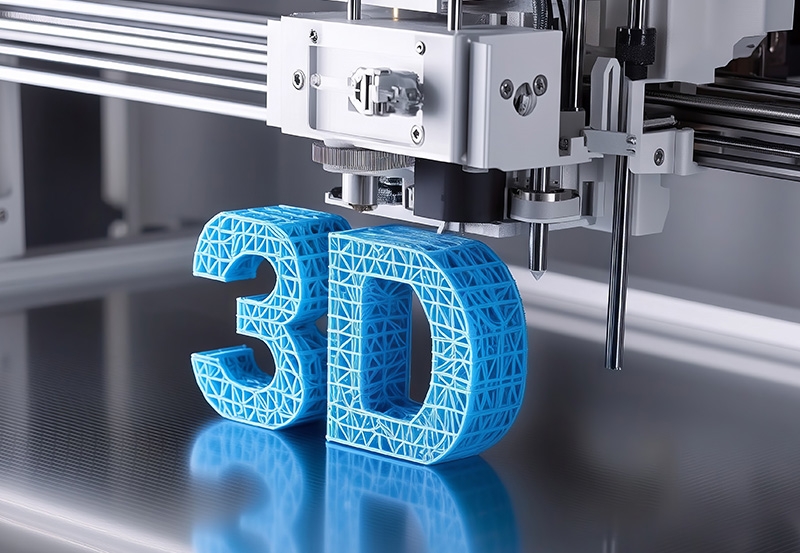
Se não é mais uma novidade absoluta – afinal, os primeiros experimentos datam do começo dos anos 1980, com aplicações industriais surgindo a partir da década seguinte –, a manufatura aditiva segue sendo uma tecnologia em franca evolução, com inovações contínuas, expansão de aplicações e muitos desafios a superar. Mais popularmente conhecida como impressão 3D, trata-se de um processo de fabricação que cria objetos tridimensionais a partir de um modelo digital, adicionando material camada por camada. Ao contrário dos métodos tradicionais da indústria, que removem material com cortes, furos e moldes, na manufatura aditiva a peça é construída do zero.
O recurso traz grandes possibilidades de design, redução de custos e aumento de produtividade. O professor e chefe do Departamento de Engenharia Mecânica da UFSC, Milton Pereira, trabalha desde 2013 com pesquisas no campo de processamento de materiais com laser, uma das técnicas utilizadas na manufatura aditiva. Para ele, o maior impacto na indústria segue sendo a disrupção. “A impressão 3D coloca a possibilidade de criar produtos e soluções muito diferentes e de alta complexidade, abrindo um grande espectro de possibilidades com materiais distintos de alto valor agregado”, avalia Pereira.
A otimização de materiais, com reaproveitamento total de sobras (quando há), e a redução notória no tempo de prototipagem e produção de peças geram enorme custo-benefício para a indústria. “Muitas empresas não estão cientes de como essas tecnologias podem ser empregadas para aprimorar seus processos, melhorar a eficiência e reduzir custos. Se os engenheiros não considerarem as possibilidades da manufatura aditiva desde o início, após a conclusão do design, as oportunidades para otimizar a produção podem ser perdidas”, diz Luís Gonzaga Trabasso, pesquisador-chefe do Instituto SENAI de Inovação (ISI) em Sistemas de Manufatura e Processamento a Laser, de Joinville.
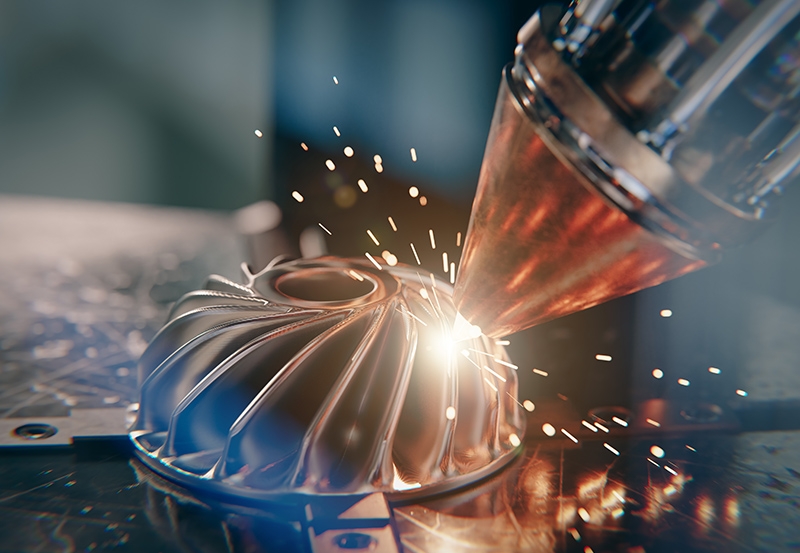
Biblioteca | Primeiro centro de processamento de metais a laser da América Latina, o Instituto de Joinville oferece uma série de soluções em manufatura aditiva, incluindo o design e produção de peças. No portfólio de clientes e parceiros incluem-se empresas como Petrobras, Furnas, Tupy e Embraer. O Instituto possui uma biblioteca digital com dezenas de peças críticas para o funcionamento de plataformas de extração de petróleo e usinas elétricas, que podem ser fabricadas a partir de aço em pó. O tempo de entrega é acelerado em muitas vezes, diminuindo prejuízos que podem chegar a US$ 2 milhões por hora, no caso da indústria de óleo e gás.
“Não se encontram peças dessas para comprar, não se contrata uma empresa para fazer, pois há longas cadeias produtivas envolvidas. Recentemente conseguimos entregar para a Petrobras uma peça em quatro dias”, conta Trabasso. Outros benefícios são a redução de emissões geradas pelo transporte e armazenamento de estoques físicos, além da manutenção de um grande inventário de peças. A tecnologia também oferece, segundo o pesquisador, outras vantagens econômicas ao permitir a produção de peças mais leves, eficientes e com menos desperdício de material.
Mesmo com tantas vantagens, a indústria nacional ainda enfrenta dificuldades para adotar a tecnologia. Além da dependência da importação de materiais, há um obstáculo de conhecimento a ser transposto. Por isso, o Instituto criou a Academia de Manufatura Aditiva, que ajuda a preparar os profissionais para utilizar as novas tecnologias. A capacitação auxilia engenheiros e projetistas a entender como podem integrar as práticas de maneira eficaz em seus processos de desenvolvimento de produtos. A Academia pode ter diferentes formatos, oferecendo cursos de várias durações, desde algumas horas até vários dias. As sessões incluem tanto teoria quanto prática, envolvendo recursos de design, análise de processos e aplicação de técnicas em projetos reais. Algumas empresas, entretanto, já avançaram bastante e têm colhido excelentes resultados, como está demonstrado a seguir.
Maior integração com clientes
Metade dos novos desenvolvimentos da metalúrgica envolveu impressão 3D.
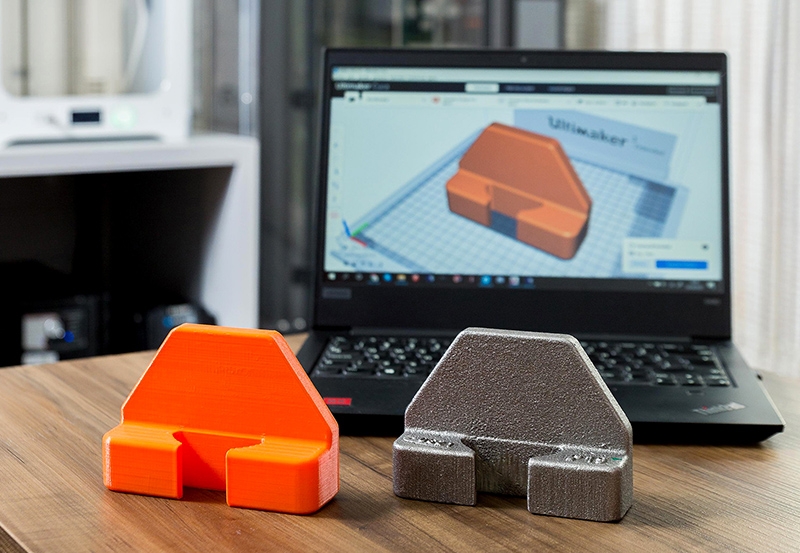
A metalúrgica Riosulense começou a utilizar manufatura aditiva para conceber produtos e ferramentais em 2020, e agora se prepara para investir cerca de R$ 2 milhões em uma máquina que imprime moldes em areia. “Essa tecnologia vai nos ajudar a ganhar mercado na parte de confecção de protótipos, para estarmos cada vez mais integrados com a engenharia dos clientes e participando do desenvolvimento de produtos”, explica Clebson Ferreira, gerente técnico da Rio.
Em 2024, pelo menos metade dos 180 novos desenvolvimentos feitos na metalúrgica para montadoras de caminhões, ônibus e equipamentos agrícolas, carros-chefes da empresa, teve alguma etapa envolvendo impressão 3D. “Com o 3D eu consigo diminuir no mínimo pela metade o tempo de prototipagem – de 60 a 120 dias para no máximo 25 – com custos bem menores. E, caso haja algo a ser melhorado ou corrigido, podemos trabalhar nisso com menos custos e mais eficiência”, avalia.
Recentemente uma bomba hidráulica teve o design validado utilizando manufatura aditiva. Uma peça conceito não funcional foi impressa, e o cliente pôde testá-la dentro de um veículo real, avaliando se mangueiras, fios e outros componentes “conversavam” adequadamente com a bomba. “Isso permite que, antes de criarmos um protótipo funcional, que exige investimentos em moldes, e a própria peça final, os problemas sejam detectados”, salienta Ferreira. Em outro case, o uso de um protótipo impresso permitiu melhorar o ângulo de um dormente para a indústria ferroviária, em um processo de redesign. O trabalho resultou em uma peça única em areia bruta, substituindo a anterior que exigia três operações de fabricação – corte, solda e usinagem. “Conseguimos reduzir custos, timing de fabricação e recursos.”
Ferramentais mais produtivos
Até 800 quilos de material por mês serão produzidos em Joinville.
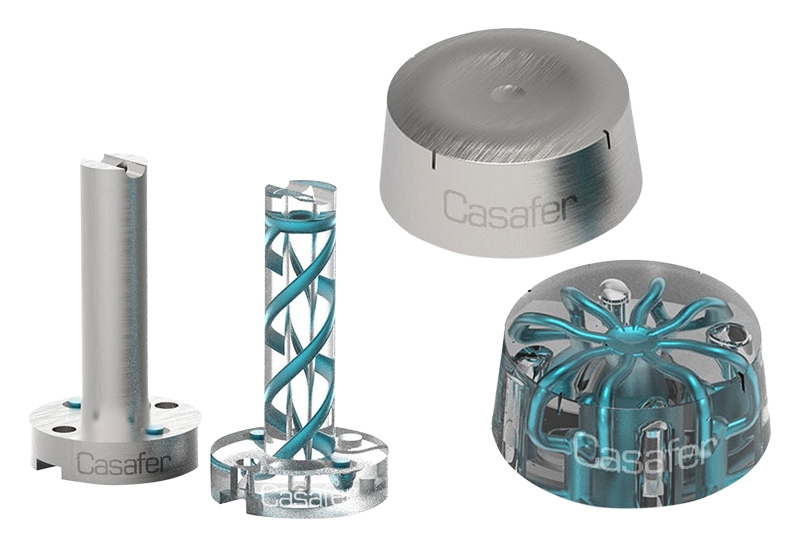
Natural de Tubarão, Allan Guimarães ainda não tinha completado 18 anos quando abriu a Casafer em Joinville, no começo de 1998. Recém-formado em Processamento de Dados pela Escola Técnica Tupy e cursando faculdade de Administração, ele percebeu uma oportunidade quando trabalhava na indústria ferramenteira da cidade. “Uma linha de produção da Consul (hoje Whirlpool) parou, com grandes prejuízos, porque não havia um pino extrator a pronta entrega na cidade. Foi preciso mandar uma pessoa de avião buscar em São Paulo. Então resolvi abrir uma empresa para fornecer esse tipo de produto para a indústria local”, conta.
Assim a Casafer se transformou em fornecedora de insumos, tecnologia e serviços para fabricantes e usuários de ferramentais e empresas de usinagem de todo o Brasil. Em 2012 Allan começou a estudar a técnica de manufatura aditiva conformal cooling (refrigeração conformada) em países como Alemanha e Itália. O conceito é relativamente simples: na indústria tradicional, a solidificação de metal através de refrigeração depende de brocas, que fazem perfurações retas e, portanto, com distâncias diferentes entre vários pontos de uma peça e, consequentemente, soluções mais limitadas de design.
Com a liberdade de design da manufatura aditiva é possível fazer furações em curvas dentro de cada peça, gerando um resfriamento mais uniforme. “O método tradicional gera problemas de deformação, de qualidade, comprometendo o tempo de vida útil do ferramental. Quanto mais rápida e uniforme a refrigeração, mais produtivo o processo. Há também menos refugo e redução de massa utilizada, gerando economia de até 40%”, enumera Guimarães.
O problema é que, em 2012, os custos para implementação da tecnologia no Brasil tornavam a ideia inviável, e a empresa só colocou a operação de pé dez anos depois. Hoje, uma empresa em Singapura e outra na Sérvia fazem os projetos para injeção de plástico e alumínio. O birô de impressão fica na China, e é de lá que a Casafer exporta parte da produção para os Estados Unidos. Neste ano a empresa vai investir R$ 10 milhões para produzir entre 500 e 800 quilos de material por mês em Joinville. “Isso era algo já planejado antes da eleição de (Donald) Trump, mas agora, com a política de restrição à China que ele deve aplicar, devemos ganhar competitividade com a fabricação no Brasil”, diz Guimarães.
Soluções para baixos volumes
Maior investimento é no aprendizado, não em máquinas.
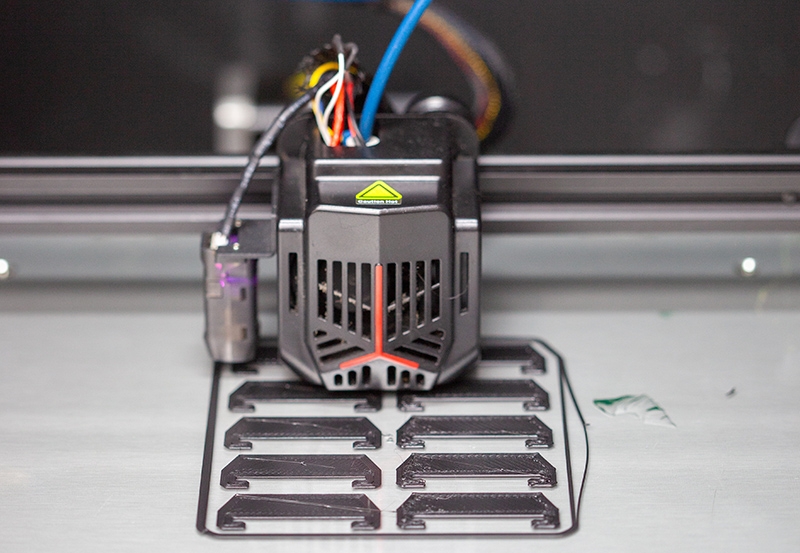
Fabricante de retificadores industriais, equipamentos para transformar corrente alternada em corrente contínua, a Provolt tem como trunfo a alta capacidade de customização. Atendendo desde o setor naval aos de mineração, óleo e gás e processamento de dados, a empresa blumenauense é uma das precursoras no Estado na produção de peças para o consumidor final, reduzindo custos em até 70% e tendo mais liberdade para desenvolver produtos exclusivos. “Para empresas que produzem pouco volume, como nós, que às vezes precisamos de apenas 20 ou 30 peças, é uma solução perfeita. Um molde para fazer injeção de uma peça custa até R$ 100 mil, e como produzimos equipamentos não seriados, o investimento muitas vezes não se justifica”, expõe o sócio-fundador da Provolt, Dieter Pfuetzenreiter.
Desde a implementação de duas máquinas de impressão 3D, em 2021, foram produzidas 65 peças, número que deve quase dobrar em 2025. Boa parte delas substitui com filamentos plásticos peças até então de metal, permitindo detalhamento e acabamento mais refinado e com custos muito menores. Mas se o investimento nos equipamentos foi baixo – menos de R$ 3 mil por máquina, segundo Pfuetzenreiter –, as horas dedicadas a entender e melhorar os processos são contadas em centenas. “As máquinas precisam de condicionamentos especiais, cada tipo de filamento tem reações específicas. O maior investimento é no aprendizado, mas esse know-how agora é nosso.”